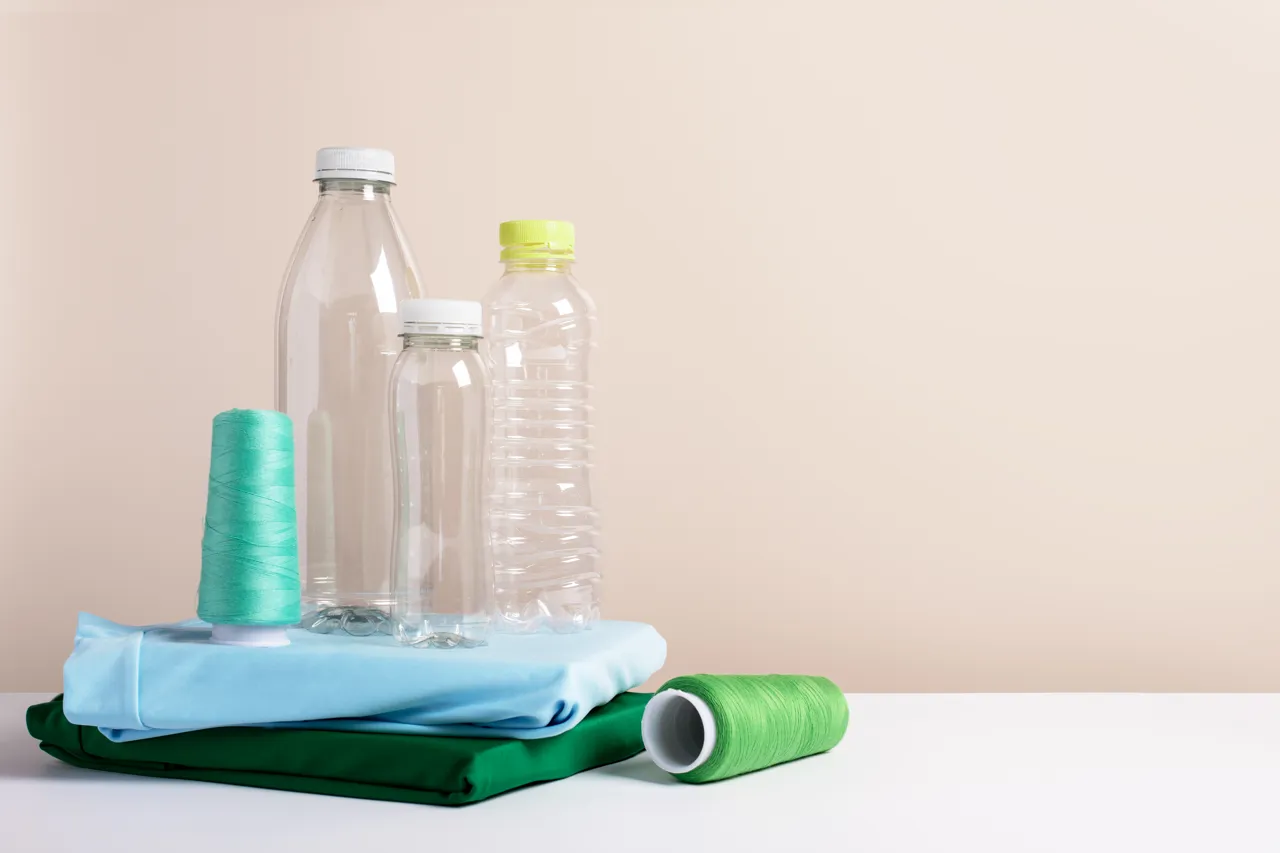
Samsara Eco fashions new future for plastic with infinite recycling tech
Ending plastic pollution with its plastic-eating enzymes
Australian company Samsara Eco is working with activewear brand lululemon to create world-leading recycled nylon and polyester garments. Samsara Eco’s innovative approach to recycling breaks plastics down to their building blocks and keeps them out of landfill.
$9.1m
CEFC commitment
World first
for nylon
Plastics
recycling
The current approach to recycling is simply inefficient and ill-equipped to handle the plastic pollution crisis we are faced with today. If we are serious about changing our ways, we need a new approach to how plastic is made and recycled. Instead of mining for fossil fuels to create new plastics or relying on current recycling methods which sees only about nine per cent actually recycled, we can take plastic that already exists and infinitely recycle it.Paul RileyCEO and Founder, Samsara
Our investment
The CEFC was an early investor in Samsara Eco in May 2022 and has committed a total of $9.1 million to support the company’s development and refinement of its enzymatic recycling technology. Climate tech specialist Virescent Ventures manages the CEFC investment.
Samsara Eco has raised more than $150 million through two successful funding rounds which have attracted investment from CSIRO deep tech fund Main Sequence, Temasek, Wollemi Capital, lulemon, Hitachi Ventures, Titanium Ventures and DVC Woolworths venture capital and innovation fund W23. Additional capital also came from Breakthrough Victoria, Assembly Climate Capital, DCVC and INP Capital.
Industry accolades
Samsara Eco has clocked up multiple innovation award wins, including:
- being named in Smart Company’s most innovative companies in sustainability for 2025
-
Australian Hero in the Energy and Renewables category at the InnovationAus 2022 Awards for Excellence.
Read more about Samsara Eco
our impact
World-first textile-to-textile recycling with lululemon
In a key milestone for textile-to-textile recycling, Samsara Eco, which has partnered with activewear brand lululemon, unveiled its world-first enzymatically recycled nylon 6,6 product in February 2024. Nylon 6,6 is commonly used for sportswear because of its durability and toughness. This durability also makes it hard to recycle.
Lululemon heralded the breakthrough as signalling “not only a turning point for sustainable innovation in apparel, but for all industries looking to shift towards more circular models.”
A first-of-a-kind plastics and textile enzymatic recycling plant using the Samsara Eco technology, is due for completion in South-East Asia in early 2028.1
Tackling a global waste issue
Global plastic use is expected to double by 2040, with the majority of plastic sent to landfill, and only 13 per cent recycled. However the mechanical recycling of plastics requires clear and clean materials, excluding millions of tonnes of coloured plastics.
Working with the Australian National University, Samsara Eco developed technology which uses enzymes to break down plastic to its core building blocks, allowing for infinite recycling.
The Samsara Eco technology can break plastic into core molecules in minutes, regardless of colour, type, or state, and can produce food-grade plastics with the same characteristics as virgin plastics.
Read our Green Files article
1. Media release, April 2025: KBR selected as key commercialisation partner for Samsara Eco’s first-of-a-kind enzymatic recycling plant